What is Abrasive Blasting?
- By Charlie Leiendecker
- •
- 06 Jul, 2017
- •
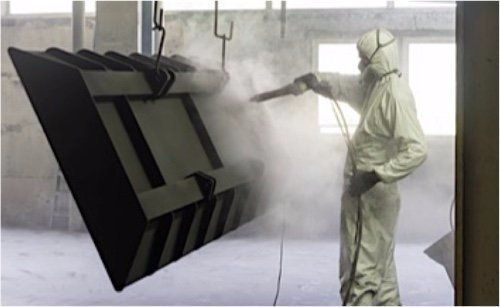
You’ve seen the results of the process in many places. It is used to refurbish old buildings and to create three-dimensional signs. It can create works of art and engrave a cemetery monument. It works well for cleaning everything from boat hulls to stone works to industrial structures. Its proper name is abrasive blasting, although it often goes by the catch-all term, sandblasting.
How Does It Work?
While the first abrasive blasting process was patented in the late nineteenth century, today’s operation is significantly more sophisticated and entails a variety of methods. Essentially, a stream of abrasive material is forcibly propelled under high pressure against a surface. The blasting material can remove rust and contaminants, smooth a rough surface, create a shape, or even make a smooth surface rough.
Either compressed air or a centrifugal wheel is typically used as the propellant, while the blasting material can be aluminum oxide, garnet, steel shot, glass, or sodium bicarbonate. Depending on the application, a more abrasive material (steel shot) or a milder version (glass beads) is used.
Either compressed air or a centrifugal wheel is typically used as the propellant, while the blasting material can be aluminum oxide, garnet, steel shot, glass, or sodium bicarbonate. Depending on the application, a more abrasive material (steel shot) or a milder version (glass beads) is used.
There Are Many Versions of the Blasting Process
Wet blasting involves an abrasive media, compressed air, and water to get the preferred finish on a surface. The addition of water to the mix results in a smooth and consistent finish. A variety abrasive media can work with this method and depends on the type of finish that’s needed.
- Bead blasting
utilizes small glass beads to remove impurities from a metal surface. It is one of the most gentle, inexpensive, and environmentally friendly methods of blasting, leaving behind no residue and posing no health or safety concerns. The beads are available in different shapes and sizes, which can provide a variety of finishes.
- Wheel blasting
is an airless process in which centrifugal force propels an abrasive against a part. It is a high velocity operation—the wheel spins at 3600 rpm—that can be used to clean large areas efficiently and quickly. Because it does not require compressed air, wheel blasting is used on bigger parts where air blasting would be too expensive. The downside of this method is that there is a limit to the type of abrasives that can be used, and the high velocity could damage certain components.
- Hydro-blasting uses pressure and a stream of water to remove any buildup without damaging the surface.
Are You Considering Abrasive Blasting For Your Next Project?
Contact Van Industries online
or call us at 610-582-1118
for more information or to request an estimate.